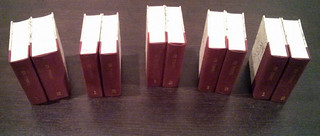
Many many thanks to both friend Suko for her copy editing time & efforts and friend Scott for the inspiration & assistance on the binding project overall. Scott has been into book binding for many years and was good on his promise of helping me out when I finally found something I wanted to print & bind. Of course, I think original promise was to assist with "a book" rather than a printing run of ten at once. Luckily Scott is the right kind of nerd in all things and seemed to enjoy as much as I the challenges & differences unique to mass production.
No irrecoverable mistakes were made! Really, the only goof was that I should have affixed my end papers BEFORE I pasted on the crash. Instead, I wound up hand trimming them and adding them in just before the covers went on. Smoother gluing of end papers to cover and better shoulder position/size would have helped things, but I assume I'll just get better at that with practice.
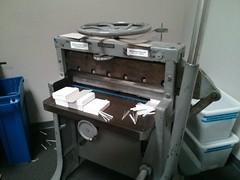

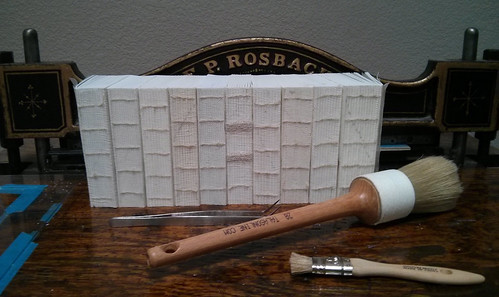
The guillotine cutter was magical and made my lame hand-bound signatures transform into some professional looking content. It also left behind little black smudges on my beautiful white paper. Luckily Scott and I had already been discussing the idea of speckling the page edges- the smudges just made it a requirement. Purple & black were selected for reasons and did an excellent job of hiding the blemishes.


Scott bravely operated the foil heat machine, facing down a number of hiccups/problems. Turns out the foil and the book cloth don't mesh well. Maybe next time leather is needed? Regardless, all of the printings look great and really gave the books an old library book vibe. Which is good.


Turns out mass-producing books takes TIME (especially when we're semi-figuring things out as we go) so after the cloth was printed & covers were cut, Scott and I parted ways as our time was up at the the Center for the Book. Great place, that. Will be going back again for classes. Knowing what I know now, will be much faster/better prepared when renting equipment/space/time in the future. Anyway, it meant the cover construction and assembly happened at home, unsupervised. I think it went pretty well.
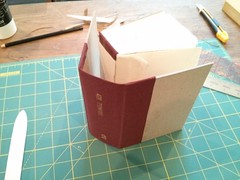


I wound up gluing most the covers on at the session in which I handed the books out. Time management. It's hard.
Knowing what I know now, I'd say the steps for the next run of books I do will be as follows:
- Determine page size & pages per signature
- Lay out book in LaTex
- Print ALL the books at once (Office Max has different bulk prices, maxing out at $0.10 per page(side) when you hit 500 pages)
- Fold & stitch signatures
- Fussy cut & glue end pages
- Glue crash
- Measure things! Have estimates!
- Rent space at the Center for the Book
- Trim pages on guillotine
- (optional)Splatter pages w/ inks
- Cut chipboard for covers on sheer
- (optional)Foil press title onto spine
- Build up spine
- Assemble cover
- Hope really hard that you didn't fuck anything up
- Affix cover to book
One of my main regrets was that I didn't take better photos throughout the process. My phone camera is pretty weak-sauce. Luckily friend Suko took some excellent photos of her books! (and if you follow either of us on other social medias, you're probably sick of seeing them over and over by now) Re-posting them here, with her permission, for prosperity:
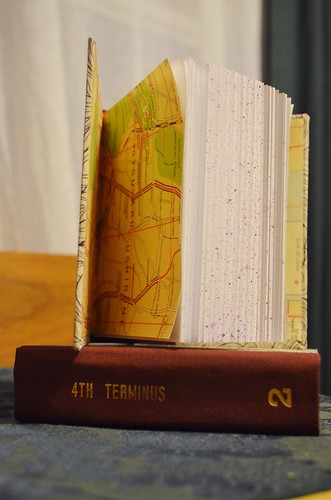
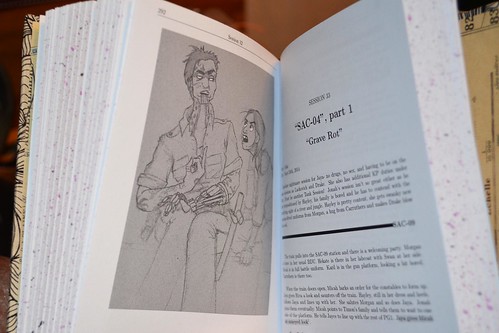

No comments:
Post a Comment